Slotted Steel Shims, as discussed in previous blogs, are simple items but there are many pains in the manufacturing process that can affect the finished product. This article deals with the problems inherent in Hot Dip Galvanizing the steel shim.
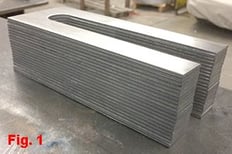
When stamped, shims should stack perfectly straight with no visible irregularities. Keeping the shims flat and straight becomes more difficult as the fingers get longer, i.e. 3” x 3” x 1/8” thick shims can be controlled much easier when struck (stamped) than 3” x 12” x 1/8” shims. Deflection is a detail of steel stamping however, tolerances can be achieved with properly designed, very sharp, well maintained tools and the correct tonnage stamping machine. (Fig. 1)
Once fabricated these perfectly flat and straight shims go to the galvanizer where it becomes difficult for them to remain this straight.
Most Hot Dip Galvanizer’s differentiate their operations into two groups based on the size of the steel product being coated known as the Large Kettle (I-Beams, Angle, Channel, etc.) and the Small Kettle/Spinner. The Small Kettle is for items small enough that many can be coated at once such as, shims, masonry anchors and smaller anchor bolts. These small items are put in wire baskets and sent through the same acid – zinc process as larger items except when lifted from the molten zinc kettle they move immediately to a high speed centrifuge where they are spun to;
- Remove any excess zinc.
- Stop the small items from sticking together as the zinc cools and hardens.
Two problems are present when Hot Dip Galvanizing Slotted Steel Shims. One is caused by the centrifuge. The basket is intentionally loaded with a batch of shims in disarray so that the acids and liquid zinc can flow freely and thoroughly coat all surfaces. When the spinner is activated the same centrifugal force that evacuates the zinc causes a lot of shifting and pressure between the shims which are interwoven amongst themselves in the basket. Adding to this problem is the temperature of the steel at the time it is being spun. While immersed in the molten zinc kettle thin Slotted Steel Shims easily reach ambient temperature of 840°F (approx. 450°C.) While mild carbon steel does not melt until it reaches 2,600°F it does reach optimal strength at approximately 230°F and above that gradually weakens as its temperature increases. At 840°F the steel has approximately 75% of its original strength. This only serves to make it more pliable and susceptible to distorting during the spinning process.
The thicker Slotted Steel Shims, such as the 1/4” and 3/8” have enough yield strength to not be affected by the temperature and centrifugal pressure. The thinner shims, such as 1/32” and 1/16” thick are bent easily, sometimes into unusable shapes.
The second problem is the stress inherent in the steel. When rolled, the steel can be straight and flat however the stress is not necessarily even throughout. As an example Fig. 2 shows a steel wedge fabricated at The Steel Supply Company. Using a low speed band saw simply cutting this shape from the original plate allows stress relief that caused it to warp.
This same stress exists in sheet metal. Its effects are compounded because almost all sheet metal is manufactured, stocked and transported in coil form. The spiral shape of the coil gets straightened to flatness +/- 1/32” per foot however the stress the coiling process introduced still exists. Stress relief can occur during the stamping process or hot dip galvanizing. Regardless, it becomes the responsibility of the shim manufacturer to examine the finished product and correct or discard any pieces that are not within tolerance. The finished Hot Dip Galvanized Slotted Steel Shim should be flat and straight so it can be installed without any interference on the jobsite. (Fig. 3)