An often overlooked issue with Slide Bearings is the system of welds. Before beginning the process the steel fabricator should understand what effect the weld will have on the Slide Bearing.
Whether Virgin Teflon®, generic PTFE or the more durable Fluorogold®, the bonding process is the same. For the purposes of this discussion we will use the most common configuration, FC-1010-CS. This is a 10 gauge (1/8” thick) carbon steel backing plate with 3/32” thick Fluorogold® Teflon® bonded to it. It is essential to assure the steel and Teflon® are bonded securely and most importantly so the bond will not decay over time. To achieve this a special 2-part epoxy is used and the steel and Teflon® are clamped together. For more on the manufacture of slide bearings, click here.
The clamped assembly is then put in an oven, heated to 450°F and held at that temperature for 4 hours. It is important to understand the role the heating process plays in the manufacture of Slide Bearings because the only real short term enemy of that bond is heat. Done improperly the welding process can create enough heat to cause the epoxy bond to melt, or “delaminate.”
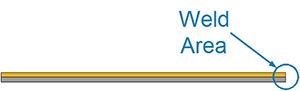
The drawing to the left (fig. 1) shows the edge of a typical Slide Bearing. Any welding will heat the steel backing plate so it is important to weld in a way that limits heat buildup.
The welding system used for Slide Bearings is sometimes left to the fabricator or called out as a “Stitch Weld” or “Seal Weld.”
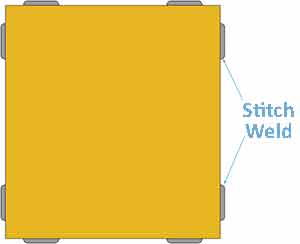
Figure 2 shows the benefit of a stitch weld which is sometimes referred to as a tack weld. By spacing out the welds heat does not build up to the point where the epoxy bond is compromised. The welder should take care to keep the length of each weld short enough to minimize heat buildup.
For most Slide Bearing applications the stitch weld is sufficient. It actually has the advantage of making the assembly easier to replace after the service life of the assembly has elapsed. As an example some pipeline work calls for a minimal stitch weld on the slide bearings. The harsh environments these pipelines pass through will cause the Teflon® or Fluorogold® surfaces to wear faster and be replaced more often. Removing a widely spaced stitch weld is far easier and less costly than a seal weld.
Fig.3 Slide Bearing Skip and Fill Weld
Figure 3 shows a seal weld in progress. When complete it will seal all the edges. In order to do this and not delaminate the Slide Bearing a Skip and Fill technique is used. The drawing shows the initial 4 welds in black, spaced so the heat does not build up in any area. The dark gray welds are done second followed by the light gray. Continuing with this Skip and Fill pattern will eventually produce a weld bead around the entire perimeter.